I built a heat exchanger a few weeks ago in an attempt to cut my heat losses from my continuous water change system: http://www.monsterfishkeepers.com/forums/showthread.php?t=411395
While the unit works, it only gave me around 25% efficiency at a max flow of 10 gallons/minute. The problem is that, in an effort to avoid copper on the freshwater side, I relied PVC to conduct the heat from the wastewater to the fresh. PVC is a very good insulator, not so good at conducting heat...
My new design uses a 1/4"x50' copper coil through which the cold incoming freshwater flows. This coil is housed in a 4"x34" piece of ABS pipe through which the warm wastewater flows. This puts the copper in direct contact with both fresh and waste water, greatly increasing the conduction over my last model.
After installing the new unit I am now getting around 67% efficiency. The outgoing wastewater is being cooled from 81 degrees to 68 degrees, while the incoming freshwater is being warmed from 63 to 75 degrees. This is at a flow of 10 gallons/minute, it gets even more efficient at lower flow rates, but I like the 50%/day water change.
The reduction in heating has been huge. I have two heat controllers on this system - one controls sump temperature and the other controls an inline heater on a 135 gallon tank in the garage. It used to be that both controllers cycled constantly, being on the majority of the time. Now they cycle much more slowly, only being on for 1/4 of the time or less.
The build started with the "head" where all the incoming and outgoing plumbing connections are. I started by cutting two discs out of 3/16" ABS sheet, one that fits tight inside the pipe and another larger one that fits the O.D.. I also cut a ring about 1/2" long from a 4" ABS cap. This was glued flush with the end of the pipe, essentially increasing the O.D. and giving me a larger surface to glue to.
After gluing the two discs together I glued in the four adapters for the incoming and outgoing lines - two 1/4" compression x 3/8" compression fittings for the freshwater, two PVC slip x 3/8" barbed fittings for the wastewater.
The coil is wrapped around a piece of PVC. This serves two purposes. First, it helps support the copper coil. Second, it directs incoming wastewater to the tail end of the pipe. Having the warm water and cold water moving in opposite directions will help with heat exchange, as the cooled outgoing wastewater contacts the cold incoming freshwater. As the incoming freshwater moves through the coil it comes in contact with warmer and warmer water, ensuring the temperature differential stays as high as possible throughout the unit. (At least that is my theory...)
Once the coil was attached to the head, it was just a matter of slipping the whole assembly into the ABS housing. An ABS disc on the tail end of the PVC coil support keeps the whole assembly centered in the 4" pipe. A 4" cap closes off the bottom end, and some aluminized bubble-wrap insulation helps reduce waste from heat loss.
I installed the new unit in series with the old one, but I may eventually tear apart my first build and reuse the coils in a new unit like this, but for now I am using them both as-is.
The glass vessel in the photo is my flow meter - I can close the drain and use a watch to calculate flow quite accurately. There is also a screen filter to prevent gunk from clogging the unit. The pressure reducing valve lowers the pressure of the incoming freshwater - this is to eliminate an annoying noise from the float valve chattering.
Overall I think this design is a good one, but I would love to hear your suggestions/critiques. Thanks for looking!
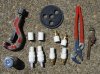
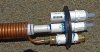
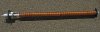
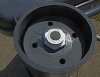
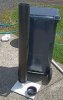
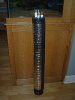
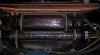
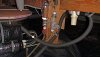
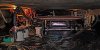
While the unit works, it only gave me around 25% efficiency at a max flow of 10 gallons/minute. The problem is that, in an effort to avoid copper on the freshwater side, I relied PVC to conduct the heat from the wastewater to the fresh. PVC is a very good insulator, not so good at conducting heat...
My new design uses a 1/4"x50' copper coil through which the cold incoming freshwater flows. This coil is housed in a 4"x34" piece of ABS pipe through which the warm wastewater flows. This puts the copper in direct contact with both fresh and waste water, greatly increasing the conduction over my last model.
After installing the new unit I am now getting around 67% efficiency. The outgoing wastewater is being cooled from 81 degrees to 68 degrees, while the incoming freshwater is being warmed from 63 to 75 degrees. This is at a flow of 10 gallons/minute, it gets even more efficient at lower flow rates, but I like the 50%/day water change.
The reduction in heating has been huge. I have two heat controllers on this system - one controls sump temperature and the other controls an inline heater on a 135 gallon tank in the garage. It used to be that both controllers cycled constantly, being on the majority of the time. Now they cycle much more slowly, only being on for 1/4 of the time or less.

The build started with the "head" where all the incoming and outgoing plumbing connections are. I started by cutting two discs out of 3/16" ABS sheet, one that fits tight inside the pipe and another larger one that fits the O.D.. I also cut a ring about 1/2" long from a 4" ABS cap. This was glued flush with the end of the pipe, essentially increasing the O.D. and giving me a larger surface to glue to.
After gluing the two discs together I glued in the four adapters for the incoming and outgoing lines - two 1/4" compression x 3/8" compression fittings for the freshwater, two PVC slip x 3/8" barbed fittings for the wastewater.
The coil is wrapped around a piece of PVC. This serves two purposes. First, it helps support the copper coil. Second, it directs incoming wastewater to the tail end of the pipe. Having the warm water and cold water moving in opposite directions will help with heat exchange, as the cooled outgoing wastewater contacts the cold incoming freshwater. As the incoming freshwater moves through the coil it comes in contact with warmer and warmer water, ensuring the temperature differential stays as high as possible throughout the unit. (At least that is my theory...)
Once the coil was attached to the head, it was just a matter of slipping the whole assembly into the ABS housing. An ABS disc on the tail end of the PVC coil support keeps the whole assembly centered in the 4" pipe. A 4" cap closes off the bottom end, and some aluminized bubble-wrap insulation helps reduce waste from heat loss.
I installed the new unit in series with the old one, but I may eventually tear apart my first build and reuse the coils in a new unit like this, but for now I am using them both as-is.
The glass vessel in the photo is my flow meter - I can close the drain and use a watch to calculate flow quite accurately. There is also a screen filter to prevent gunk from clogging the unit. The pressure reducing valve lowers the pressure of the incoming freshwater - this is to eliminate an annoying noise from the float valve chattering.
Overall I think this design is a good one, but I would love to hear your suggestions/critiques. Thanks for looking!

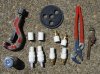
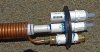
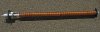
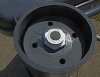
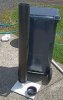
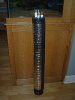
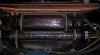
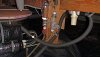
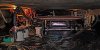