After months of researching, planning, designing and redesigning I'm finally ready to start this project. It's going to be pretty different from most of builds on here in a couple of ways. For one thing, it's going to hold a lot less water than some of the builds, so I shouldn't have to deal with some of the complex issues of bracing and support associated with the real monster builds. But the fact that it's a paludarium is going to raise a bunch of different issues, such as ventilation and drip system.
Anyways, on to the specs:
The tank is going to be plywood/glass. Dimensions are 60.5"L X 28"W X 41.5" tall. Water depth will be around 15", so overall volume will be about 100gal.
The tank will be viewable from the front and right side. The casing is going to built from 3/4" birch plywood. The right side window is going to be a single piece of 3/8" glass. The bottom part of the front is going to have a 15" tall piece 1/2" glass and is going to have a braceless top edge. I'm going to add sliding door track onto the top edge of the bottom piece and have 2 pieces of 1/8" glass as sliding doors so that the upper part of the tank will be accessible from the front.
Filtration will be a 40gal sump with returns through spraybars at the substrate and surface of the water section, and along the top of the back and left side feeding a dripwall. I'm going to be carving styrofoam branches that will be partly submerged and partly emersed and planted with epiphytes. I'm going for a lush rainforest look and am going to be putting a lot of effort into the scaping. I should warn you now though, that it's probably going to be quite a while before this thing is up and running.
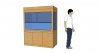
Anyways, on to the specs:
The tank is going to be plywood/glass. Dimensions are 60.5"L X 28"W X 41.5" tall. Water depth will be around 15", so overall volume will be about 100gal.
The tank will be viewable from the front and right side. The casing is going to built from 3/4" birch plywood. The right side window is going to be a single piece of 3/8" glass. The bottom part of the front is going to have a 15" tall piece 1/2" glass and is going to have a braceless top edge. I'm going to add sliding door track onto the top edge of the bottom piece and have 2 pieces of 1/8" glass as sliding doors so that the upper part of the tank will be accessible from the front.
Filtration will be a 40gal sump with returns through spraybars at the substrate and surface of the water section, and along the top of the back and left side feeding a dripwall. I'm going to be carving styrofoam branches that will be partly submerged and partly emersed and planted with epiphytes. I'm going for a lush rainforest look and am going to be putting a lot of effort into the scaping. I should warn you now though, that it's probably going to be quite a while before this thing is up and running.
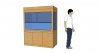